Main Content
Silica based hierarchically porous monoliths
We work on the rational design and preparation of sol–gel and porous glass based silica monoliths with hierarchical structure for high-pressure/high-performance solid–liquid operation in chromatography and catalysis. Hierarchically porous silica monoliths (Figure 1, with interskeleton macropores and intraskeleton mesopores) offer more degrees of freedom in their design than conventional particulate fixed-bed adsorbers, separators, and reactors from the local pore scale up to the bulk material scale. This allows to combine adsorption/reaction selectivity, mobile phase velocity (analysis speed; contact time), heat and mass transfer (efficiency; residence time distribution), as well as specific surface area (loading capacity) in a unique manner. As highlighted by the "magic triangle" (Figure 2) the monoliths simultaneously offer
(i) a large specific surface area Aspec, i.e., loading capacity for adsorption and/or reaction typical for packings of (small or large) fully porous particles;
(ii) short diffusion lengths Ldiff in spatial domains where transport is diffusion-limited and where adsorption and/or reaction occurs, reflecting the properties of small fully porous or larger core–shell particles with a thin porous shell; and
(iii) a hydraulic permeability realized only with relatively large (fully porous or core–shell) particles, i.e., a large characteristic flow length Lflow.
In addition to their "equivalent packings" of core–shell particles (regarding the possibility to independently adjust Ldiff and Lflow), the silica monoliths have a larger specific surface area as well as a larger external surface area. The latter represents a larger contact area between flowing and stagnant fluids, which intensifies heat and mass transport to and from the active surface sites. With tailored skeleton thickness, macroporosity, and macropore size highly efficient and selective monolithic separation columns and flow-through microreactors are envisioned; sub-micrometer macropore size and skeleton thickness guarantee negligible backmixing and strong driving forces for mass transfer, heat transfer, and reaction.
We therefore focus on the preparation of monoliths featuring sub-micrometer macropore size and skeleton thickness. Success in this regard relies on a multiscale morphological and mass transport characterization (Figure 3), which allows us to establish quantitative synthesis–morphology–transport relationships for rational, very flexible material design.
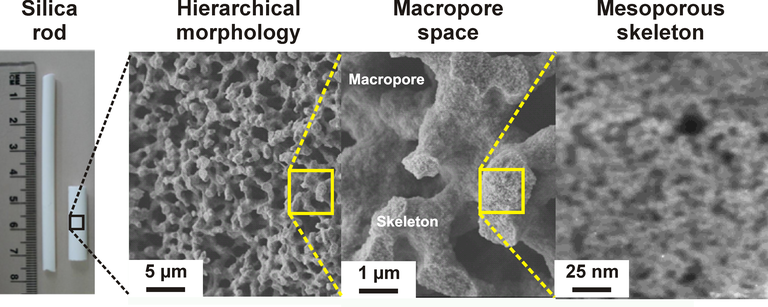
Figure 1. Pore space morphology of macroporous–mesoporous silica monoliths. The macropores form an interskeleton network of flow-through channels, dedicated to advection-dominated transport through the monolith (usually realized by pressure-driven flow) and towards the much smaller intraskeleton mesopores, in which mass transfer remains diffusion-limited.
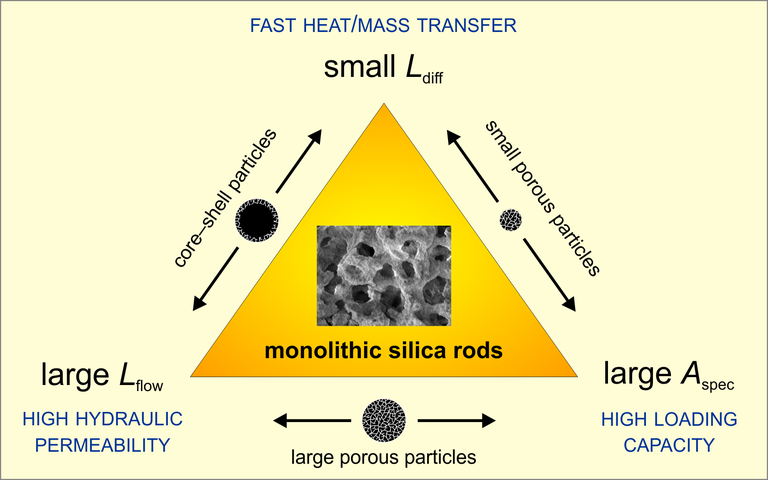
Figure 2. "Magic triangle" for particle-packed beds, addressing hydraulic permeability (flow-channel size), heat/mass transfer resistance (diffusion length), and the adsorption/reaction capacity (specific surface area). With respect to packings of small or large, fully porous or core–shell particles, silica monoliths offer access to new regions in the design space. And compared to packings of core–shell particles with equivalent flow and diffusion lengths the silica monoliths present a larger specific surface area (allowing higher loading capacity) as well as a larger external surface area, i.e., a higher contact area between flowing and stagnant fluids, which intensifies mass transport to and from the active surface sites and heat removal by convection.
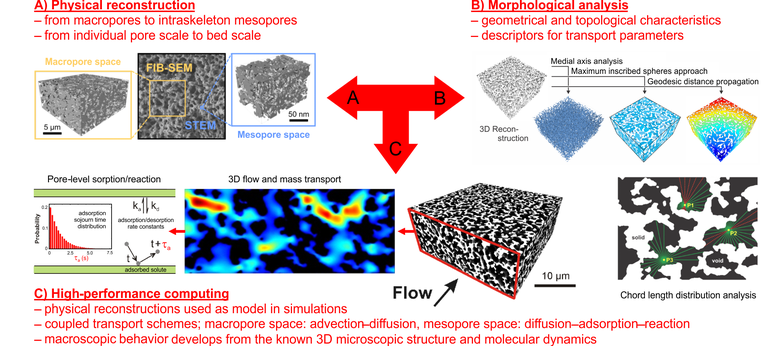
Figure 3. Approach to quantitative preparation–morphology–transport–functionality relationships for silica monoliths (functional porous materials, in general). (A) The preparation of monoliths with addressable morphology and functionality is followed by physical reconstruction of the hierarchical pore structure using advanced imaging methods. (B) Morphological properties are quantified with statistical methods, which ideally provide also descriptors of relevant transport phenomena, e.g., of diffusive mass transfer resistance in the skeleton of a monolith or of backmixing in its macropore space. (C) Numerical simulation of hydrodynamics, mass transport, adsorption, and reaction in the (physically reconstructed) hierarchical pore structure. In the macropore (flow-through) space the three-dimensional velocity field is calculated with the lattice-Boltzmann method, while tracer motion in the velocity field is simulated using a random-walk particle-tracking method. In the mesopore space, sorption and reaction can be implemented by a microscopic stochastic approach.
Highlighted publications:
- C.P. Haas, T. Müllner, R. Kohns, D. Enke, U. Tallarek
High-performance monoliths in heterogeneous catalysis with single-phase liquid flow.
Reaction Chemistry & Engineering 2017, 2, 498–511. DOI: 10.1039/C7RE00042A - M. von der Lehr, K. Hormann, A. Höltzel, L.S. White, A.E. Reising, M.F. Bertino, B.M. Smarsly, U. Tallarek
Mesopore etching under supercritical conditions – a shortcut to hierarchically porous silica monoliths.
Microporous and Mesoporous Materials 2017, 243, 247–253. DOI: 10.1016/j.micromeso.2017.02.036 - D. Enke, R. Gläser, U. Tallarek
Sol–gel and porous glass-based silica monoliths with hierarchical pore structure for solid–liquid catalysis.
Chemie Ingenieur Technik 2016, 88, 1561–1585. DOI: 10.1002/cite.201600049 - D. Stoeckel, C. Kübel, M.O. Loeh, B.M. Smarsly, U. Tallarek
Morphological analysis of physically reconstructed silica monoliths with submicrometer macropores: Effect of decreasing domain size on structural homogeneity.
Langmuir 2015, 31, 7391–7400. DOI: 10.1021/la5046018 - K. Hormann, U. Tallarek
Analytical silica monoliths with submicron macropores: Current limitations to a direct morphology–column efficiency scaling.
Journal of Chromatography A 2013, 1312, 26–36. DOI: 10.1016/j.chroma.2013.08.087 - D. Hlushkou, K. Hormann, A. Höltzel, S. Khirevich, A. Seidel-Morgenstern, U. Tallarek
Comparison of first and second generation analytical silica monoliths by pore-scale simulations of eddy dispersion in the bulk region.
Journal of Chromatography A 2013, 1303, 28–38. DOI: 10.1016/j.chroma.2013.06.03